In today's fast-paced and customer-centric market, the customization of manufacturing services is pivotal for success. Artificial Intelligence (AI) agents are at the forefront of this transformation, offering personalized experiences and streamlining services to meet the unique needs of each customer. They are not just reshaping interactions but also ensuring that the manufacturing processes are more efficient and responsive to market demands. This article explores the various facets of how AI is enhancing custom manufacturing, from personalizing customer interactions to achieving operational excellence.
Key Takeaways
- AI agents personalize the manufacturing experience by learning customer preferences, managing order inquiries, and providing tailored maintenance advice.
- The scalability of AI enables manufacturers to meet customer demands efficiently, particularly during periods of rapid business growth.
- AI-driven systems enhance quality assurance and maintain consistency by automating routine checks and analyzing production data.
- Operational excellence is achieved through AI's capabilities in streamlining paperwork, predicting demand, and managing inventory effectively.
- Appinventiv's custom AI solutions are pivotal in transforming manufacturing operations, driving advancements with AI/ML innovations, and providing competitive IT consulting.
The Impact of AI on Custom Manufacturing
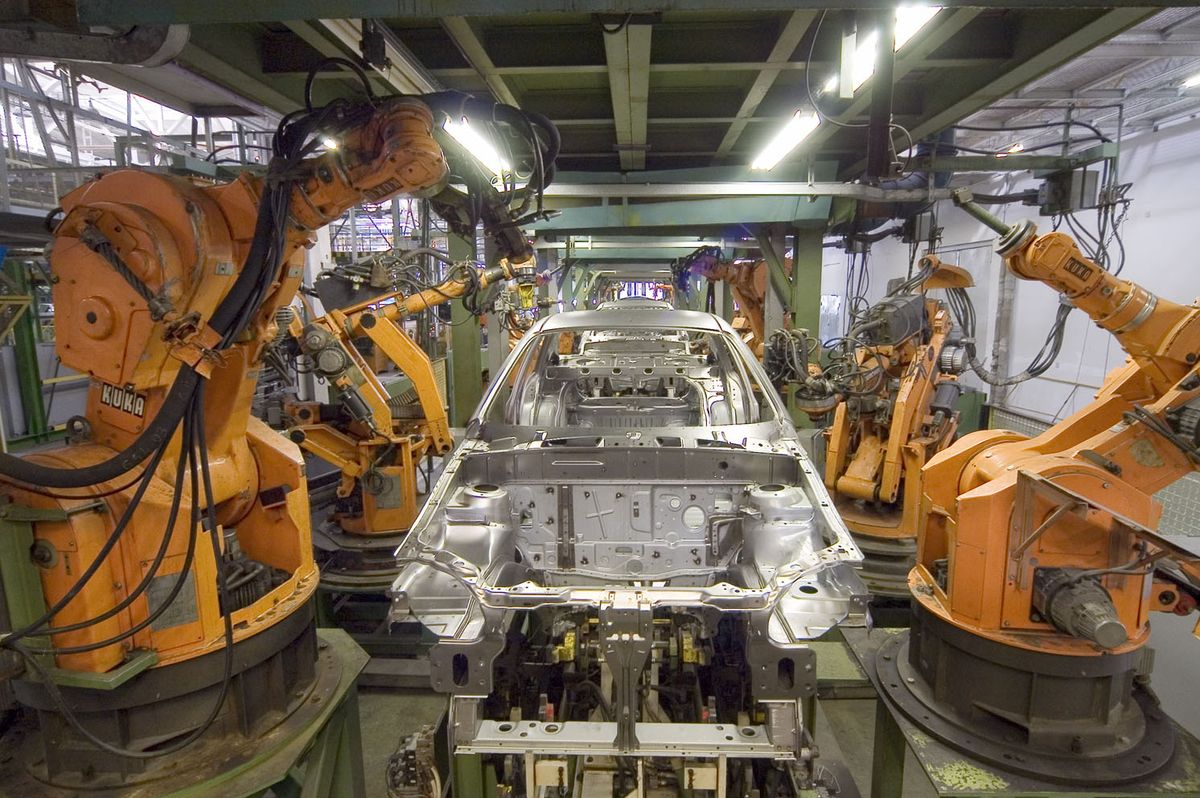
Personalized Interactions and Customer Satisfaction
In the realm of custom manufacturing, AI has revolutionized the way businesses interact with their customers, ensuring a highly personalized experience. By leveraging customer data, AI agents can tailor interactions to individual preferences, leading to increased satisfaction and loyalty.
- Personalized Customer Service: AI enables the automation of customer service, providing timely and relevant responses.
- Faster Support Handling: With AI, support queries are handled more efficiently, reducing wait times.
- Email Marketing Personalization: Customers receive offers and content aligned with their interests and purchase history.
Embracing AI in customer interactions not only enhances the customer experience but also sets the stage for a more intuitive and responsive manufacturing service.
The integration of AI into customer service workflows allows for a more dynamic and engaging approach to customer relations, fostering a sense of value and appreciation that is crucial for long-term business success.
Scalability and Meeting Customer Demands
In the realm of custom manufacturing, scalability is a cornerstone of success. AI solutions are pivotal in ensuring that businesses can not only meet but exceed customer expectations, which are constantly on the rise. A Salesforce report highlights that 72% of customers now expect faster service than ever, underscoring the urgency for scalable solutions.
AI-driven systems are designed to handle the increasing volume of data and complexity that comes with business growth. They adapt to changing demands with ease, ensuring that manufacturers can provide service in a more efficient and scalable manner. For instance, Norck's implementation of AI in custom production showcases how AI helps manufacturers forecast demand and adapt output, which is crucial for maintaining a lean inventory and guaranteeing product availability when clients need it.
The integration of AI in manufacturing processes is not just about keeping up with the trends; it's about setting a new standard of operational excellence and surpassing industry standards.
The benefits of AI in scalability extend beyond just meeting customer demands; they also include the ability to explore new opportunities in a competitive landscape. With advanced algorithms and scalable infrastructure, businesses are well-equipped to handle the pressures of rapid growth and the high turnover rates that can plague the service sector.
Quality Assurance and Consistency
In the realm of custom manufacturing, quality assurance (QA) is paramount. AI has ushered in a new era of precision and reliability, transforming the way manufacturers approach QA. By integrating AI-driven systems, companies can now automate and enhance various testing procedures, including functional, automation, security, and performance testing.
The implementation of AI in quality control processes ensures uniformity and accuracy in evaluating the finished product. For instance, AI-powered computer vision algorithms are capable of analyzing images or videos of products with exceptional precision, identifying defects and deviations from quality standards that might elude human inspectors.
AI's data-driven approach to quality control enables manufacturers to make informed decisions and implement preventive measures, significantly elevating the consistency of the final product.
Moreover, AI-powered quality control (QC) systems are not only adept at finding flaws but also play a crucial role in monitoring manufacturing processes in real-time. This allows for immediate adjustments, maximizing efficiency and reducing waste, thereby guaranteeing consistency in the final product.
AI-Driven Operational Excellence in Manufacturing
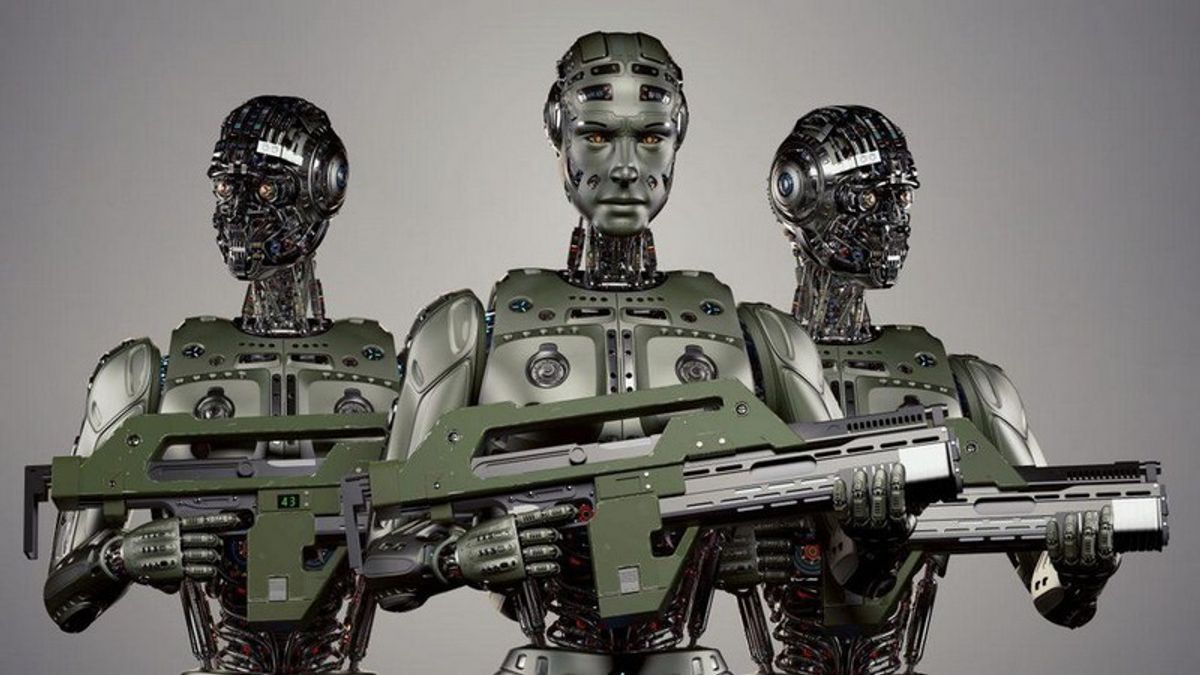
Streamlined Paperwork and Administrative Efficiency
The integration of AI and machine learning (ML) technologies in manufacturing has revolutionized the way paperwork is handled. Robotic Process Automation (RPA) is now at the forefront, transforming purchase orders, invoices, and quality control reports from burdensome tasks into streamlined processes. This shift not only reduces the time spent on manual entries but also minimizes errors, leading to more efficient operations.
By automating administrative tasks, companies can focus on more strategic activities that enhance their competitive edge.
Here's a glimpse of how AI-driven automation is changing the landscape:
- Invoice Automation: Speeding up the billing cycle
- Payment Automation: Ensuring timely transactions
- Document Automation: Simplifying record-keeping
- Compliance Documents: Maintaining regulatory standards
- Supply Chain Document Automation: Optimizing logistics
These advancements in automation are not just about efficiency; they're about reshaping the entire customer experience. With AI, businesses can now manage customer communications more effectively, leading to increased loyalty and engagement.
Predictive Demand Analysis and Inventory Management
The integration of AI into inventory management systems marks a significant leap forward in custom manufacturing. AI-driven predictive analytics play a pivotal role in enabling businesses to make informed decisions. By analyzing historical sales data, market trends, and external factors, companies can anticipate demand fluctuations and proactively adjust inventory levels. This not only reduces the risk of stockouts or excess inventory but also ensures optimal resource allocation.
For example, machine learning (ML) algorithms can identify patterns in data to forecast demand with high accuracy. An automotive parts manufacturer might use these models to predict the need for spare parts, optimizing inventory while cutting costs. Similarly, a fashion retailer could leverage AI to analyze social media trends, weather forecasts, and customer preferences to ensure popular items are always in stock.
The strategic use of AI for inventory management results in a more agile and responsive supply chain, capable of adapting to market dynamics efficiently. It's a transformative approach that aligns production with consumer demand, fostering a leaner and more competitive manufacturing environment.
Connected Factories and Integrated Systems
The advent of connected factories represents a significant leap forward in the manufacturing sector. By harnessing the power of artificial intelligence, these factories become intelligent ecosystems capable of self-regulation and advanced decision-making. Real-time data analysis from machinery, facilitated by AI, allows for predictive maintenance, operational streamlining, and minimized downtime, thanks to the integration of IoT sensors.
In such an interconnected environment, machine-to-machine communication is not just a possibility but a daily reality. This communication enables rapid adjustments to production schedules, aligning with fluctuating demand and ensuring that operations remain fluid. The result is a manufacturing landscape that is not only more efficient but also more responsive to the needs of the market.
The transformative impact of AI in manufacturing extends to order fulfillment and supply chain management. The IBM Watson Order Optimizer is a testament to how AI can refine complex processes, leading to better supply chain responsiveness and smarter decision-making.
Moreover, the digital twin technology allows for a virtual representation of manufacturing facilities, pinpointing areas of energy loss and opportunities for performance enhancement. This level of insight is invaluable in driving down costs and elevating productivity. AI's role in warehouse management further underscores its value, optimizing inventory and streamlining order fulfillment to create more efficient and cost-effective operations.
Revolutionizing Customer Service with AI Agents
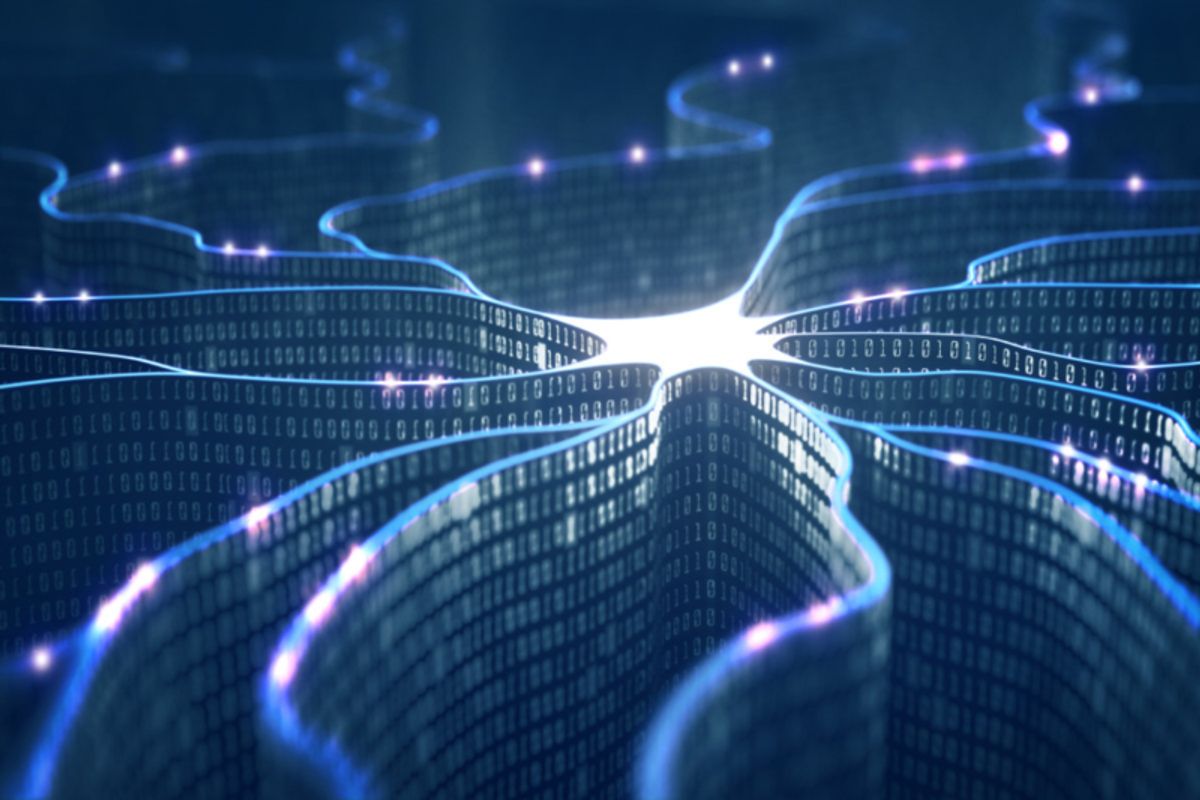
Enhanced Customer Experience through AI Chatbots
The integration of AI chatbots in customer service is a game-changer for custom manufacturing. AI chatbots are revolutionizing the way businesses interact with customers, providing immediate responses and personalized assistance. This not only enhances the customer experience but also streamlines the service process.
AI chatbots are capable of handling a multitude of customer inquiries simultaneously, ensuring that no customer is left waiting. This efficiency is crucial in maintaining high levels of customer satisfaction and brand loyalty.
The benefits of AI chatbots extend beyond customer interaction. They also play a pivotal role in optimizing operations. By managing routine inquiries, chatbots allow human agents to concentrate on more complex issues, thereby improving overall service quality. The following points highlight the multifaceted advantages of AI chatbots in customer service:
- Personalized Product Recommendations: Tailoring experiences to individual preferences.
- Marketing Messages: Delivering targeted communications that resonate with customers.
- Operational Efficiency: Reducing resolution times and operational costs.
- Proactive Service: Anticipating customer needs and addressing them preemptively.
Optimizing Operations for Reduced Downtime
In the realm of custom manufacturing, downtime is a critical factor that can significantly impact productivity and profitability. AI agents play a pivotal role in minimizing these costly interruptions. By harnessing the power of predictive analytics, these intelligent systems can foresee and mitigate potential disruptions before they escalate into major issues.
The integration of AI into manufacturing operations is not just about preventing problems; it's about creating a seamless, efficient production flow that adapts to changing conditions and maintains a high level of operational excellence.
Manufacturers are now leveraging AI to automate manual processes, which not only resolves errors but also enhances supply chain visibility. This leads to a substantial improvement in operational efficiency, often quantified in increased KPIs. The table below illustrates the impact of AI on key operational metrics:
By continuously analyzing data and optimizing processes, AI-driven systems ensure that manufacturers can deliver their service in a more efficient and scalable manner. This proactive approach not only drives efficiency but also supports data-driven decision-making, fostering innovation in product development.
Deeper Engagement with Personalized Support
AI agents are revolutionizing customer support by offering deeper engagement through personalized interactions. By analyzing customer data, AI can tailor support to individual needs, ensuring that each interaction is relevant and effective. This approach not only enhances customer satisfaction but also fosters loyalty and trust.
- Personalized Offers: AI-driven systems can send personalized offers based on purchase history and preferences, significantly improving the customer experience (CX).
- Marketing Campaigns: Tailoring marketing efforts to individual clients creates more meaningful connections and longer-lasting relationships.
- Predictive Actions: AI can anticipate future customer actions, allowing businesses to proactively address needs and preferences.
With the integration of AI in customer support, companies are witnessing a surge in revenue growth, attributed to the personalized and automated customer experiences they are able to provide.
The table below illustrates the key aspects of personalized customer support enhanced by AI:
Appinventiv's Role in Advancing Manufacturing with AI
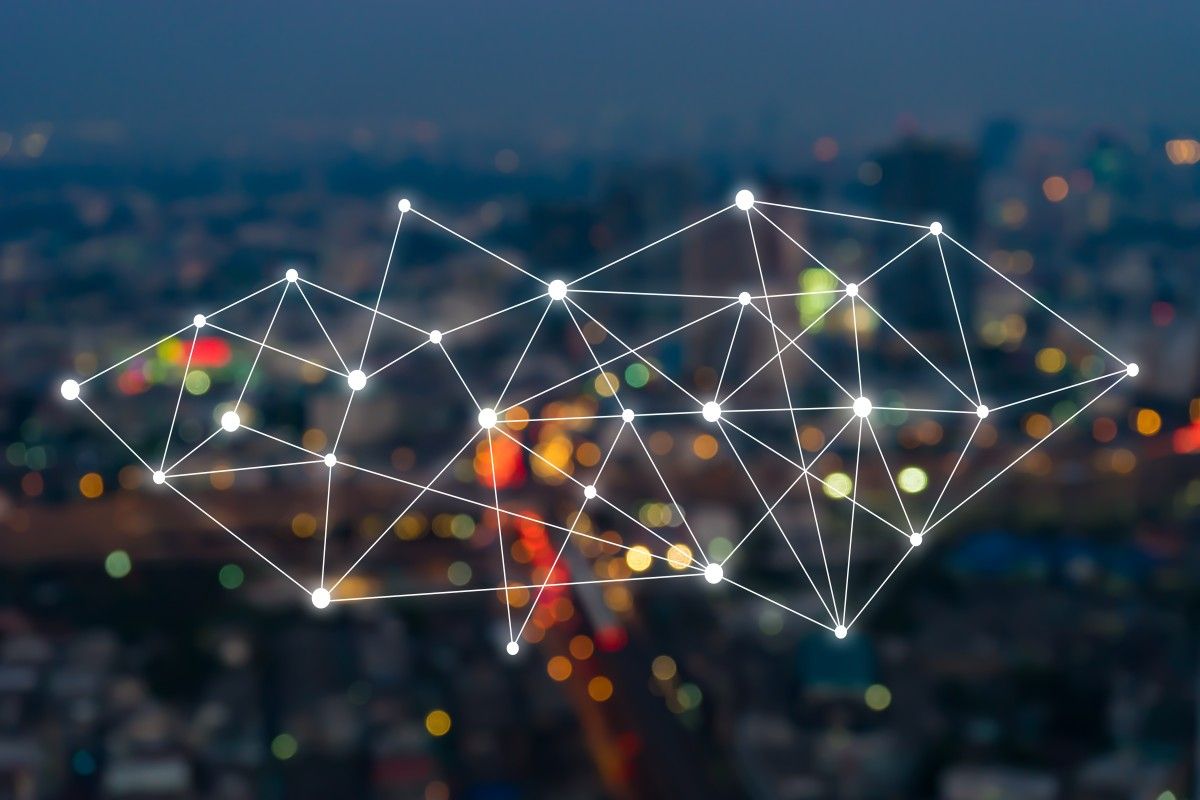
Custom AI Solutions for Manufacturing Excellence
Appinventiv's approach to custom AI solutions is transforming the manufacturing landscape, offering a strategic edge to businesses seeking to modernize operations. By automating repetitive tasks and providing data-driven insights, these solutions enhance the effectiveness of order management systems, accelerate decision-making, and ensure a customer-centric fulfillment process.
The application of AI across various manufacturing use cases, such as predictive maintenance and supply chain optimization, has led to significant improvements in efficiency, accuracy, and cost-effectiveness. Manufacturers now have the opportunity to embrace AI as a means to revolutionize traditional processes and maintain competitiveness in the market.
Embracing AI in manufacturing is not just about technology adoption; it's about redefining the entire business model to be more responsive, efficient, and customer-focused.
The following list highlights key areas where Appinventiv's AI solutions make a substantial impact:
- Quality Assurance
- Streamlined Paperwork
- Demand Prediction
- Order Management
- Connected Factories
Assembly line optimization and warehouse management have also seen considerable advancements, with AI integration making these areas more efficient and cost-effective.
Transforming Operations with AI/ML Innovations
The integration of AI and ML technologies is pivotal in transforming operations within the manufacturing sector. These innovations are not just about automation; they're about enabling smarter, more efficient, and highly adaptive processes. For instance, AI-driven analytics convert complex data into actionable insights, fostering data-driven decision-making and a competitive edge.
- Advanced analytics for predictive models and data visualizations
- Optimized inventory management through predictive analytics
- Enhanced demand forecasting to adjust production schedules
By harnessing the power of AI and ML, manufacturers can anticipate market changes, optimize operations, and reduce waste, leading to significant cost savings and improved customer satisfaction.
However, the challenge lies in selecting the right AI technologies that align with specific business goals. Azure AI Services, for example, offers a suite of tools that can be tailored to enhance operational efficiency and innovation. The key is to leverage these tools in conjunction with expert consulting services to maximize their potential.
Collaborative IT Consulting for Competitive Edge
In the realm of custom manufacturing, collaborative IT consulting plays a pivotal role in maintaining a competitive edge. By partnering with experts in the field, companies can leverage a wealth of knowledge and experience to optimize their operations. This partnership often involves a comprehensive analysis of current systems, followed by the implementation of strategic IT solutions that propel the business forward.
- Dynamics 365 Support
- SAP Consulting
- Strategic IT Solutions
- SaaS Development and Consulting
These services are not just about support; they are about creating a roadmap to success with solutions that are adaptable, secure, and capable of propelling your business into the future. The goal is to transform operations with cutting-edge technologies, such as AI and ML innovations, ensuring that the software development services evolve your business idea into a successful growth story.
Embracing a collaborative approach to IT consulting can significantly enhance a company's ability to innovate and respond to market changes swiftly and effectively.
Frequently Asked Questions About AI in Manufacturing
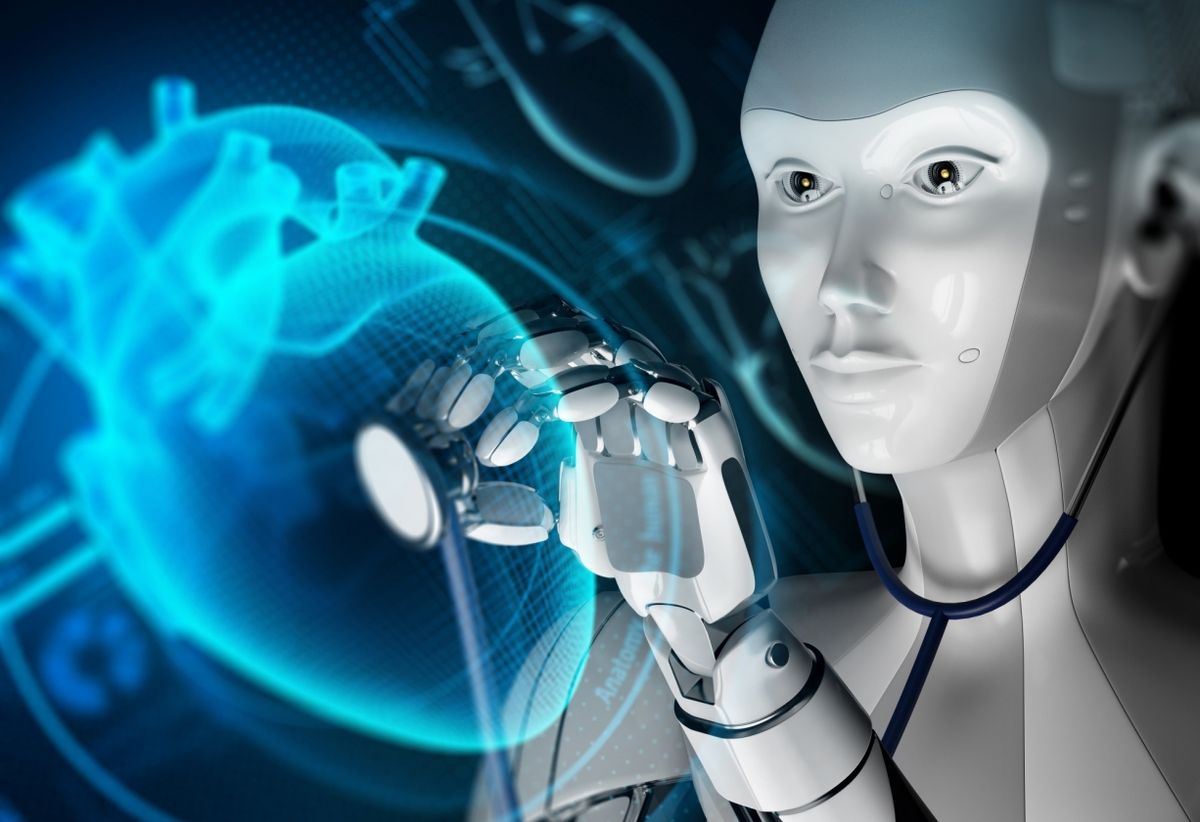
How AI is Used in Manufacturing
Artificial Intelligence (AI) is fundamentally altering the landscape of manufacturing. Manufacturers are leveraging AI to enhance operational efficiency, customize product designs, and forecast financial outcomes. AI's role in manufacturing is multifaceted, with applications ranging from predictive maintenance to optimizing supply chains and improving quality control.
- Predictive Maintenance: AI analyzes equipment data to anticipate faults, reducing downtime.
- Supply Chain Optimization: AI streamlines logistics, managing inventory levels efficiently.
- Quality Control: Advanced algorithms ensure product consistency and detect defects early.
- Demand Forecasting: AI predicts market demands, allowing for better production planning.
Embracing AI represents a strategic move for manufacturers aiming to modernize operations and maintain a competitive edge. The transformative approach offered by AI is reshaping traditional manufacturing processes, driving innovation, and enhancing productivity across the entire lifecycle.
The Benefits of AI for Custom Manufacturing Services
The integration of artificial intelligence (AI) in custom manufacturing services has been a game-changer for the industry. AI's ability to process and analyze large datasets rapidly allows manufacturers to gain valuable insights into market trends, customer preferences, and competitive landscapes. This leads to more informed product development and ensures that new offerings are in line with market demands.
AI's diverse applications, including predictive maintenance and supply chain optimization, have transformed traditional manufacturing processes. Manufacturers who adopt AI technologies are strategically positioning themselves for modernization and competitive advantage. The benefits are clear: enhanced efficiency, reduced costs, improved product quality, and optimized inventory management.
The transformative impact of AI extends across the entire manufacturing lifecycle, driving innovation and productivity at every stage.
Here are some of the key benefits:
- Data-driven decision-making: Leveraging machine learning for market analysis.
- Operational efficiency: Streamlining production processes and quality control.
- Cost-effectiveness: Reducing waste and predicting maintenance needs.
- Innovation: Fostering a culture of continuous improvement and staying ahead of the curve.
Future Trends in AI-Enhanced Manufacturing
As we look to the future, the role of AI in manufacturing is poised to grow exponentially, with several key trends emerging that promise to further revolutionize the industry. The integration of AI with the Internet of Things (IoT) is expected to create smarter, more connected factories, where every device and machine communicates seamlessly, leading to unprecedented levels of efficiency and productivity.
- Predictive Quality Assurance: Leveraging historical and real-time data to preemptively address quality issues.
- Warehouse Management: AI-driven optimization of inventory and order fulfillment processes.
- Assembly Line Optimization: Enhanced efficiency and reduced waste through intelligent automation.
- Predictive Maintenance: Minimizing downtime by predicting equipment failures before they occur.
Embracing these trends will not only streamline operations but also empower manufacturers to offer highly personalized products and services, meeting the ever-evolving demands of the market. The future of manufacturing is not just about automation; it's about creating a symbiotic relationship between AI and human ingenuity to foster innovation and growth.
Conclusion
In conclusion, the integration of AI agents in custom manufacturing is not just a trend but a strategic transformation that is reshaping the industry. By offering personalized interactions, scaling with demand, and enhancing quality assurance, AI is enabling businesses to provide superior customer experiences and optimize operations. The insights provided by AI-driven analytics empower businesses to make informed decisions, streamline paperwork, and predict future demands. As we have explored, Appinventiv's custom AI solutions exemplify the potential of AI to revolutionize manufacturing, ensuring that enterprises can meet the challenges of a dynamic market. With the continued evolution of AI tools, the future of customer service automation and manufacturing excellence looks bright, promising a more efficient, responsive, and customer-centric industry.
Frequently Asked Questions About AI in Manufacturing
How is AI used in custom manufacturing?
AI is used in custom manufacturing to offer tailored customization options, manage order inquiries efficiently, provide maintenance tips, and enhance overall operational efficiency through automation and data analysis.
What are the benefits of AI for custom manufacturing services?
The benefits of AI in custom manufacturing include personalized customer interactions, scalability to meet fluctuating demands, improved quality assurance, and streamlined paperwork and administrative tasks.
How do AI agents enhance customer satisfaction?
AI agents enhance customer satisfaction by learning customer preferences, providing personalized support experiences, and offering real-time assistance, which leads to increased loyalty and sales.
What role does AI play in inventory management and demand prediction?
AI plays a critical role in inventory management by optimizing supply chains and predicting maintenance needs, which reduces operational costs and downtime. It also helps in demand prediction to manage inventory more efficiently.
How can Appinventiv's custom AI solutions benefit manufacturing companies?
Appinventiv's custom AI solutions can help manufacturing companies by integrating AI into their processes for supply chain management, predictive maintenance, and overall operational excellence, leading to improved efficiency and cost-effectiveness.
What are the future trends in AI-enhanced manufacturing?
Future trends in AI-enhanced manufacturing include the development of connected factories with integrated systems, the use of cobots for collaborative automation, and the continuous innovation in AI/ML solutions to further optimize manufacturing processes.